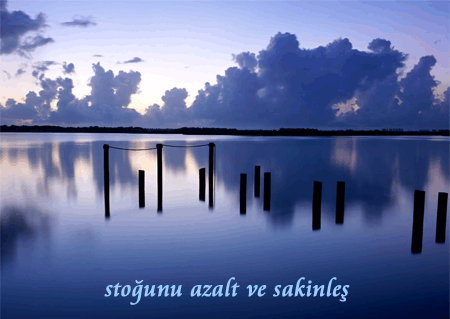
Stokların şişkin olması iyi mi kötü mü, azaltılmalı mı yoksa azaltılmamalı mı ? … Bu soruya farklı zamanlarda farklı cevaplar almak mümkün, ancak genelde elimizde stok olacağına ?para? olması daha iyidir.
Stok kelimesi farklı bölümler tarafından farklı algılanır. Bu dökümanda ?stok?, işletmenin hammadde, yarı mamul, mamul, işletme malzemesi, hurda … olarak sınıflandırabileceği her türlü malzeme veya nesne olarak düşünülmelidir.
İlk kısımda yer alan önerilerimizi oldukça basit bulabilirsiniz, bu basitlik sizi yanıltmasın çünkü gerçekleştirilmeleri çok etkili sonuçlar yaratır.
Stoklarımızı azaltmak için yapılabilecekleri 4 ayrı gruba bölmüş olabiliriz :
* Hiç Para Harcamadan Yapılabilecekler
* Kısa Dönem?de Yapılabilecek Olanlar
* Orta Vadede Yapılacaklar
* Uzun Vadede Yapılacaklar
Hiç para harcamadan neler yapabilirsiniz … işte en çok işe yarayacak liste :
* Önce içeri girişi durdurun (siparişleri iptal ederek, teslim tarihi değiştirerek …)
* Bundan sonra net ihtiyacınız olmayanı sipariş etmeyin
* Elinizdekileri satmaya çalışın
* Fazla olanı gerekirse maliyetine satın
* Diğerinin yerine kullanın, gerekirse bunun için yeniden operasyon yapın
* İhtiyaç dışı kalanı maliyetin altına satın
* Satamadıklarınızı YOK Edin
.
Gördüğünüz gibi bu kısımda hiç para harcamıyorsunuz ama stoğunuz azaldığı için elinizdeki para artıyor. Şimdi daha planlı bir çalışma gerektiren ikinci adımı atabilir ve ?kısa dönemde yapılabilecekleri? gerçekleştirebilirsiniz.
Kısa dönemde, hemen neler yapmalısınız …
* Çek Defterini elinize alın ve Kısa Dönem Çalışmaları bitene kadar bırakmayın. Özellikle ?A? sınıfına giren envanterler için gerekçe sorun, anlatılanı sonuna kadar dinleyin (problemler hakkında fikir verecektir), bu tür malzemeler için bütün anlaşmaları ve çekleri siz imzalayın.
Envanterin azaltılması için sorumluluk ve görev verin. Ekibinizde Satınalma, Lojistik, Satış, Üretim bölümü çalışanları mutlaka olmalı. (Bu iş asla stajyerlerin işi değildir)
Hedef koyun ve hedfi herkesin bilmesini sağlayın. Kendinize stok için hedefler saptayın (x günlük envanter gibi), bunu iş arkadaşlarınız ile paylaşın. Bu arada gerçekleşen ve planlanmış olanı sürekli karşılaştırın
Ekibiniz HIZLI bir envanter ve problem analizi yapmalı. Önce Açık Üretim ve Satınalma siparişlerini gözden geçirin, mevcutları değil. Çünkü önce hareketi kontrol altına almalı ve kanamayı durdurmalısınız. ABC analizi ve önemli ? önemsiz listesi gibi yöntemler kullanın.
Depo ve Lokasyon denetimi yapın. Kayıp envanter her zaman problem yaratır, bulmanın en kolay yolu içeride gezinmektir. Herhangi bir lokasyona gidin, orada bulunan malzemelerin KODLARINI (saymanıza gerek yok) not edin, geriye dönüp bilgisayarınız ile karşılaştırın. Sonuçlar sizi şaşırtıyor ise doğru yoldasınız…
Darbeyi hızlı indirebilirseniz iyi olur. Fazla ve kullanılamayacak olanları tespit etti iseniz bunları nasıl yok edebileceğinizi Üst Yönetim, Finans ve Muhasebe ile tartışın. Yok etmek SEVİMLİ GÖZÜKMESE DE çoğu zaman en iyisidir.
Orta vade içinde neler yapmalısınız
Bu dönemde yapılacaklar için daha fazla disiplin ve analiz gerekli. Diğer yandan şu ana kadar pek ihtiyaç duymadığınız bilgi sisteminize bu kısımda ihtiyaç duyacaksınız.
Orta vade içinde yapılabilecekler 5 adımda özetlenebilir :
Darboğazları genişletin. Stoklarınızın azalmasını engelleyen darboğazlar vardır. En önemlileri tedarikçilerinizin izlediği politikalar, şirket içi alışkanlıklar ve prosedürler, bilgi sisteminizin gereken desteği sağlayamaması, kullanılan ekipman ve üretim merkezlerinin teknik özellikleri sayılabilir.
Stoklarınızı enine boyuna analiz edin. Stoklarınızı farklı bakış açıları ile incelemelisiniz. Örneğin ?güvenlik stoğu? yüksek olanlar niçin yüksek, değeri yüksek olanların devir hızı tatminkar mı, temin süresi uzun olanlar nasıl daha kısa sürede temin edilebilir gibi sorgulamalar yapmalısınız.
Stok kayıtlarınızın doğruluğu için çalışın. Kayıtlarınız doğru değilse işiniz çok zor, bunun için sisteminizin içindeki tüm envanter hareketleri sınıflanmalı, hata kaynakları belirlenmelidir. Bunun yanında ürün ağaçları ve rotaların doğruluğu en üst düzeye çıkartılmalı, kısmı sayım tekniği ile sistem desteklenmelidir.
Prosedürlerinizi ve kurallarınızı yazın. Çalışanlarınızın tümü için bir kılavuz olmalı çünkü herkesin aynı şeyi aynı şekilde bilmesi ve yapması gerekir. Sizin için ?zaten öyle olması gereken? başkaları için ?öyle? olamayabilir.
En iyisi stok sisteminizin kurallarını yazmaktır.
Optimize etmeye çalışın. Tüm stok sisteminizi tek seferde optimize edebilecek herhangi bir yöntem yoktur. Onun için stoklarınızı bu amaca uygun sınıflamanız ve türlerine göre farklı politikalar geliştirmeniz gerekir.
MRP veya MRP-II yöntemlerini devreye almak, kararsız kalınan malzemeler için ise ?azaltma? yöntemini uygulamak netice verebilir.
Uzun vadede ne yapabilirsiniz
Unutmamanız gereken en önemli şey ?stoğun kendiliğinden azalmayacağı? ve ?sebepler ortadan kalkmadan herhangi bir azalmanın kalıcı olmayacağıdır?. Bu nedenle sebepleri yok etmek için hangi yöntem uygun ise o kullanılmalıdır.
Ana yol haritası olarak ?Yalın Üretim ? Lean Manufacturing? ilkelerinin izlenmesi hemen hemen her durum için geçerlidir. Bazı kaynaklarda yöntemlerin birbirlerinin karşıtı gibi gösterilmesi sizi yanıltmasın çünkü bunların büyük kısmı bazı terminolojik veya akademik kaygılardan doğmaktadır.
Uzun vade içinde yapılması gereken ?formal? veya ?sistematik? yöntemleri devreye alarak stoklarınızın bir daha yükselmemesini sağlamak ve firmanın rekabetçi pozisyonunu korumasını temin etmektir.
Bunun için ana yöntemlere konsantre olmanız gerekir.
Malzeme ve üretim planlama alanında MRP ve MRP-II yöntemleri, akışın yönetimi alanında KANBAN veya diğer ?çekme yöntemleri?, sistemin sağlıklı ve çevik kalabilmesi için 5S ve SMED uygulamaları, üretim alanındaki iş sıralarının tespiti için çeşitli SCHEDULING yaklaşımları, talebin yönetimi için farklı tahmin algoritmaları, teslim tarihi yönetimi için uygulanabilecek basit veya karmaşık yöntemlerin hepsi çözülecek probleme göre seçilmelidir. Bunlardan herhangi biri ne tüm problemi çözer ne de birinin kullanılması diğerini engeller.